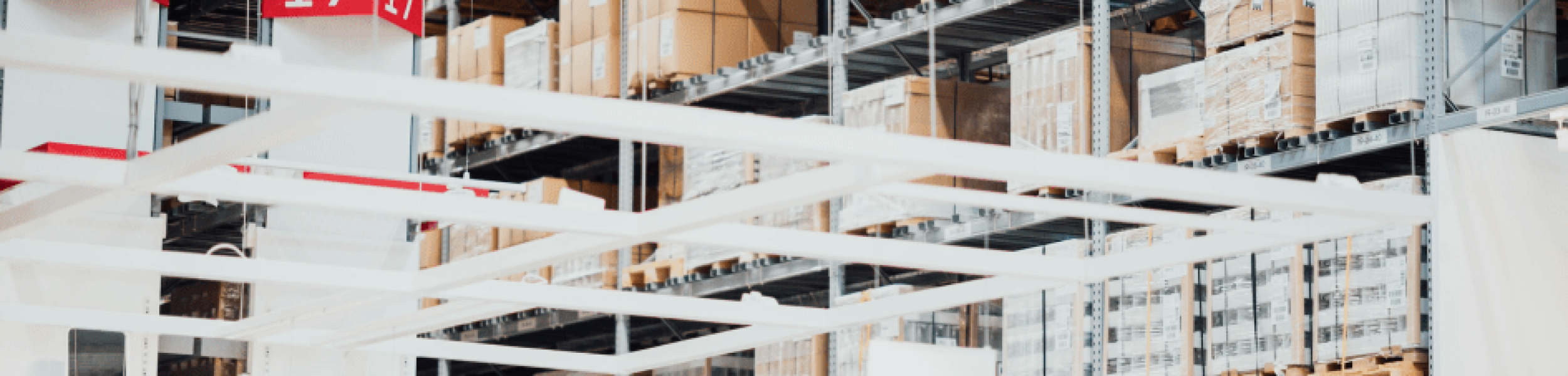
Warehouse space optimization: KPG Wholesale case study
- Parcels are stored randomly, resulting in wasted warehouse space.
- Labor time is spent on finding parcels, affecting profit margins.
Read a short case study from our customer, KPG Wholesale in Estonia, who uses Parcelcube in their new, larger warehouse.
A case study
KPG started looking for a parcel measuring system when they combined their small warehouses into one big one. “In smaller warehouses, there was no need to measure parcels; we would just look for a space and later find the parcel with more or less ease. However, our old system would not have worked in our bigger warehouse.
Looking for empty spaces and later finding parcels is a huge waste of time without an automated system. Instead, we now measure all parcels. The system calculates how many parcels fit on the shelves and indicates where enough room exists to fit them.”
KPG Head of System Development says: “Parcelcube is a great system for us, it would be very challenging to manage the warehouse parcel system without it. In addition to time and warehouse space savings, what we value most is that it’s so easy to use. You set it up once, and then it just works.”
More efficient storage with the help of Parcelcube 900
Use the help of Parcelcube 900 to make your storage more efficient:
- Place the package on the device: Simply place the item on the Parcelcube.
- Quick measurements: Parcelcube measures the dimensions and weighs the item in less than 1 second.
- Integration with logistics software: Parcelcube software links item dimensions to the item ID and integrates with your logistics software, ensuring all data is captured and utilized efficiently.